Scaling workforce without losing quality: Techniques to maintain quality while expanding team size

Previous article: Staff augmentation for outsourcing companies 101
Growth is exciting, but it can be daunting. As your business expands, the pressure for scaling workforce often clashes with the need to maintain exceptional quality. This indeed can leave you wondering: how do you scale your team effectively without sacrificing the high standards that have made you successful?
This article dives into a toolbox of practical strategies to help you navigate this challenge. We'll explore techniques for attracting top talent, fostering a culture of quality, and streamlining onboarding processes. By implementing these strategies, you can build a larger, more skilled and easily-scaling workforce that fuels continued growth without compromising on quality.
Staff augmentation for outsourcing companies 101
- Scaling workforce without losing quality — you are here
- Communication in teams and cross-cultural team management
- Building successful relationships with foreign customers
- Using data analytics in human resources for better decisions
- Data leakage prevention in hybrid teams
Foundations of quality in scaling workforce
Quality standards and benchmarks
Defining and upholding quality standards is crucial for successful project delivery, especially when scaling operations. Here are the key aspects:
- Determining quality standards. Quality refers to the degree to which a product or service meets specified requirements and customer expectations. It includes factors such as functionality, reliability, usability, efficiency, maintainability, and portability. A comprehensive Quality Management Plan (QMP) should outline these standards, metrics, processes, and responsibilities, aligning with the organization's quality policy and stakeholder requirements. Therefore, specific quality metrics should be defined to measure and track various aspects of quality:
- Defect rates. Track the number of defects per unit of production using tools like Six Sigma. Analyze defect types and frequencies to identify problem areas.
- Customer satisfaction. Measure through surveys, Net Promoter Scores (NPS), and customer feedback platforms. Use scores and feedback trends to gauge satisfaction levels and areas for improvement.
- Performance. Assess using key performance indicators (KPIs) like production speed, uptime, and throughput. Utilize dashboards to monitor these metrics in real time.
- Regulatory compliance. Ensure adherence to industry standards through regular audits and compliance checks. Use compliance software to track and document adherence to regulations like ISO 9001 or GDPR.
- Upholding quality during scaling. Continuous monitoring and improvement processes are essential to uphold quality. So implementing tools like control charts, Pareto analysis, and root cause analysis helps identify trends, prioritize issues, and recommend improvements. Establish robust quality assurance processes to ensure adherence to standards, and use quality control mechanisms to identify and address defects in deliverables. Standardize processes, procedures, and templates to maintain consistency.
Assessment of current quality controls
Evaluating and improving quality control mechanisms is crucial when scaling operations to support a larger workforce. Here are the key steps:
- Existing quality control mechanisms. Evaluate current processes by mapping out workflows, identifying bottlenecks, and gathering feedback from employees. For instance, use Statistical Process Control (SPC) charts to monitor production quality and identify deviations.
- Identify areas for improvement. Check the consistency of quality control processes across different teams, locations, or product lines and standardize where possible. Assess opportunities for automating manual quality control tasks, such as inspections, data collection, and reporting, to improve efficiency, consistency, and accuracy. In conclusion, evaluate training programs and competency levels of quality control personnel, identifying gaps that may impact quality.
Review documentation and traceability processes to ensure they are well-documented and data can be easily traced back to its source. Assess the effectiveness of current technology and tools used for quality control, considering upgrades or new implementations, such as statistical process control software or real-time monitoring solutions. - Implement improvements. Optimize quality control processes by eliminating redundancies, streamlining workflows, and implementing best practices. Firstly, develop and implement comprehensive training programs to upskill quality control personnel. Secondly, foster a culture of continuous improvement through employee involvement, regular process reviews, and best practice implementation. Finally, strengthen supplier and vendor management processes to ensure incoming materials meet quality standards. Implement robust quality assurance processes and regular audits to monitor the effectiveness of quality control mechanisms and identify areas for further improvement.
Strategic staff augmentation
Role of staff augmentation in quality control
Staff augmentation can be a game-changer for boosting quality control processes, especially during times of rapid growth or when you're facing resource shortages. Here’s how it supports quality control:
- Bridging skill gaps. With staff augmentation, you can bring in specialized quality control pros who have the exact expertise or certifications your projects need. This ensures that quality standards are upheld, even if your internal team is stretched thin.
- Flexible staffing. It lets you adjust the size of your quality control team based on the demands of your projects or seasonal needs. This means quality control activities are well-staffed without the long-term commitment of permanent hires.
- Access to best practices. Providers often have seasoned quality control professionals who carry best practices and knowledge from various industries. As a result, this can help you refine your processes and stay aligned with industry standards.
- Focused expertise. By adding dedicated quality control professionals to your team, you ensure these crucial activities get the attention they need, without overloading your existing staff.
- Rapid deployment. These providers can swiftly bring in quality control experts for urgent projects, product launches, or unexpected gaps, ensuring your quality control efforts remain consistent during critical times.
- Cost-effectiveness. Opting for staff augmentation can be more cost-effective than hiring full-time employees, especially for short-term or project-based needs. You sidestep the overhead costs of permanent hires while still maintaining high quality standards.
Selecting high-quality talent
Choosing high-quality augmented staff is essential for maintaining project quality standards. Here are key criteria to consider:
Rigorous screening and vetting processes. A comprehensive screening process includes several steps:
- Technical assessments. Use coding challenges, technical interviews, and practical tests to evaluate the candidate's skills. For example, employ platforms like HackerRank for coding assessments.
- Background checks. Conduct thorough checks on employment history, educational credentials, and professional references. Therefore, use third-party services to verify the accuracy of the information provided.
- Cultural fit assessment. Evaluate candidates' communication styles, work ethics, and teamwork capabilities through behavioral interviews and personality tests. Tools like the DiSC profile assessment can be used for this purpose.
Proven track record and references
- Client testimonials and case studies. Review client testimonials and case studies to gain insights into the quality of the provider's augmented talent and project delivery.
- Industry recognition and awards. Consider providers with industry recognition or awards, indicating their commitment to quality and customer satisfaction.
- References and audits. Request references from past clients and inquire about any third-party audits or certifications the provider has undergone.
Continuous training and skill development
- Training programs. Evaluate the provider's investment in continuous training and skill development for their augmented talent.
- Knowledge sharing and mentorship. Inquire about the provider's approach to knowledge sharing and mentorship, which can enhance the quality and expertise of the augmented staff.
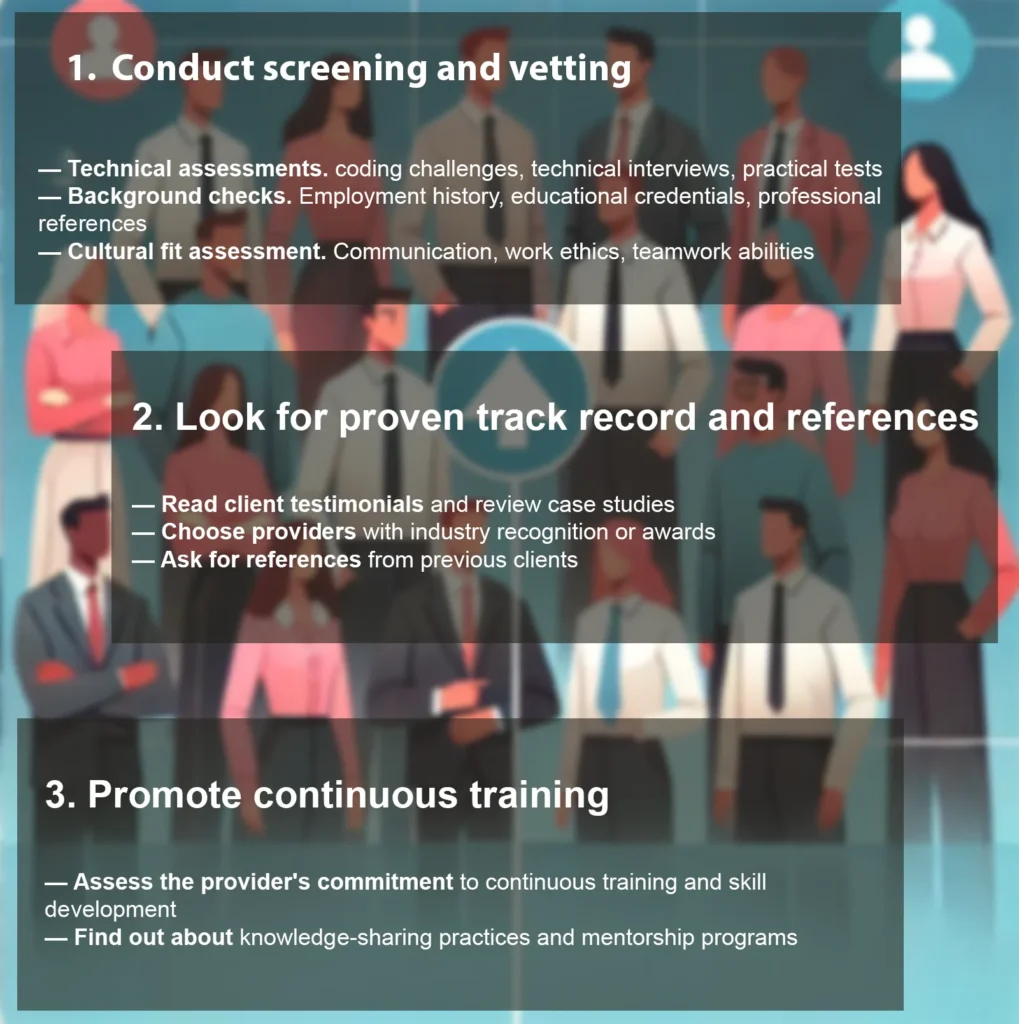
Choosing high-quality augmented staff
Staff augmentation enables businesses to rapidly scale their teams up or down by onboarding or offboarding augmented staff as required. This scalability ensures that the right level of resources is available at any given time.
Quora user
Choosing top-notch staff for scaling your workforce is crucial for keeping your project quality standards high. Here are some key criteria to keep in mind:
Rigorous screening and vetting processes
A thorough screening process is essential and includes multiple steps:
- Technical assessments. Use coding challenges, technical interviews, and practical tests to gauge the candidate's skills. Platforms like HackerRank are great for coding evaluations.
- Background checks. Dig deep into employment history, educational credentials, and professional references. Third-party services can help verify all the information provided.
- Cultural fit assessment. Evaluate how candidates communicate, their work ethics, and teamwork abilities through behavioral interviews and personality tests. Tools like the DiSC profile assessment can be handy for this.
Proven track record and references
Look for providers who have a solid history of delivering quality:
- Client testimonials and case studies. Read client testimonials and review case studies to understand the provider's capability in delivering high-quality augmented talent.
- Industry recognition and awards. Choose providers with industry recognition or awards, as these often reflect a commitment to quality and customer satisfaction.
- References and audits. Ask for references from previous clients and check if the provider has undergone any third-party audits or holds relevant certifications.
Continuous training and skill development
Ensure the provider invests in their staff’s ongoing improvement:
- Training programs. Assess the provider's commitment to continuous training and skill development for their augmented staff.
- Knowledge sharing and mentorship. Find out about their knowledge-sharing practices and mentorship programs, which can significantly boost the quality and expertise of the augmented staff.
Technology and tools for quality assurance
Leveraging technology in quality management
Using advanced technology is essential for enhancing quality management processes, especially when scaling your workforce and operations. Here are some key technological tools and strategies:
Automation and real-time monitoring
Automated inspection systems and sensors can detect defects and deviations from quality standards in real-time during production. This reduces human error and enables immediate corrective actions. Real-time data collection and analysis tools help monitor quality parameters, identify patterns, and make data-driven decisions for continuous improvement.
Advanced analytics and artificial intelligence (AI)
Leveraging advanced analytics tools and AI algorithms allows organizations to analyze vast amounts of quality data from multiple sources. This enables early detection of potential quality issues and predictive maintenance. AI and machine learning models optimize quality control processes, predict future quality trends, and recommend corrective actions. In addition, these tools can predict in advance the most appropriate time for your next workforce scaling.
Digital quality management systems
Implement systems like QMS software that include the same or similar features:
- Centralized data repositories. Store all quality-related data in one accessible location.
- Automated workflows. Streamline processes like document control, audit management, and corrective actions.
- Real-time analytics dashboards. Provide visual insights into quality metrics and trends.
- Compliance tracking. Automate compliance checks and ensure adherence to industry standards.
Supplier and customer collaboration
Digital platforms and cloud-based solutions facilitate sharing quality specifications, tracking supplier performance, and promptly addressing quality issues with suppliers and customers. Natural language processing and sentiment analysis gather and analyze customer feedback, identifying areas for quality improvement.
Quality training and documentation
E-learning platforms, virtual reality simulations, and digital documentation systems provide comprehensive quality training to employees, ensuring adherence to standards. Augmented reality (AR) overlays and digital work instructions guide employees through complex quality procedures, reducing errors.
By leveraging these technological advancements, organizations can streamline quality management processes, enhance data-driven decision-making, improve collaboration, and foster a culture of continuous quality improvement in terms of their operations and workforce scaling.
Data analytics for quality control
Data analytics is vital in enhancing quality control processes, especially when scaling operations. Here’s how organizations can leverage data analytics for quality control:
Defect analysis and root cause identification
Collect and analyze data from production lines, inspection reports, and customer feedback to identify patterns and trends in defects. Use statistical techniques like control charts, Pareto analysis, and regression analysis to pinpoint root causes, whether related to materials, processes, equipment, or human factors. Implement predictive analytics models to forecast potential quality issues and take preventive measures.
Real-time data collection and monitoring systems
Examples include:
- Manufacturing Execution Systems (MES). Track and document the transformation of raw materials to finished products in real time.
- IoT sensors. Monitor parameters such as temperature, humidity, and pressure during production to ensure they stay within specified limits.
- SCADA systems. Supervisory Control and Data Acquisition systems monitor and control industrial processes, collecting data on operational parameters and providing real-time feedback.
Critical quality parameters
Track parameters such as defect rates, cycle times, yield rates, and equipment performance metrics. Use tools like SPC charts to ensure these parameters stay within control limits.
Supplier quality management
Collect and analyze data on supplier performance, including defect rates, on-time delivery, and compliance with specifications. Use data analytics to identify high-risk suppliers or batches, enabling targeted inspections or corrective actions. Implement supplier rating systems based on data-driven performance metrics to support supplier selection and management decisions.
Quality cost analysis
Capture and analyze data on quality-related costs, such as inspection, rework, scrap, warranty claims, and customer returns. Use cost-benefit analysis and optimization techniques to identify areas where quality improvements can lead to significant cost savings. Quantify the financial impact of quality initiatives and prioritize investments based on potential return on investment (ROI).
Continuous improvement and knowledge management
Establish a centralized data repository for quality data, enabling cross-functional collaboration and knowledge sharing. Use data visualization tools and dashboards to effectively communicate quality performance metrics and trends to stakeholders. Leverage data analytics to identify best practices, benchmark against industry standards, and drive continuous improvement initiatives.
Training and development
Continuous training programs
Continuous training programs are essential for maintaining a skilled and adaptable workforce, especially during periods of scaling. Here’s how to implement effective continuous training initiatives:
Benefits of continuous training
- Addresses emerging skill gaps. Keeps the workforce updated with industry trends, new technologies, and evolving business needs.
- Fosters lifelong learning. Encourages ongoing professional development and cultivates a culture of continuous improvement.
- Enhances employee engagement. Increases motivation and retention by investing in employees' growth.
- Improves productivity. Boosts efficiency and overall work quality through updated skills and knowledge.
- Positions as industry leader. Helps the organization stay ahead by continually innovating and adapting.
Strategies for effective implementation
- Needs assessment and goal setting:
- Conduct regular skills assessments to identify gaps.
- Define clear, measurable learning objectives aligned with organizational goals.
- Promote a learning culture:
- Recognize and reward learning achievements.
- Encourage knowledge sharing through presentations and mentoring.
- Provide access to learning resources like online libraries and industry publications.
- Lead by example, with leaders actively participating in training.
- Leverage technology and flexible delivery:
- Utilize eLearning platforms, virtual simulations, and mobile apps.
- Implement microlearning modules for bite-sized, on-demand learning.
- Incorporate AI and analytics to personalize training and track progress.
- Continuous improvement and adaptation:
- Regularly review and refine training programs based on feedback and data.
- Adapt content and delivery methods to align with evolving needs.
- Foster a culture of continuous improvement by encouraging employee involvement.
Developing a culture of quality
Creating a work environment where quality is a shared responsibility and a core company value requires a multi-faceted approach:
Leadership commitment and accountability
- Visible commitment. Senior leadership must champion quality as a top priority and demonstrate their commitment through actions and resource allocation.
- Clear goals and accountability. Establish clear quality goals, metrics, and accountability measures aligned with the organization's strategic objectives.
- Empowerment. Empower employees at all levels to take ownership of quality and make decisions that uphold quality standards.
Employee engagement and empowerment
- Involvement in quality initiatives. Involve employees in defining quality standards, processes, and improvement initiatives to foster a sense of ownership.
- Comprehensive training. Provide training on quality principles, tools, and best practices to equip employees with the necessary knowledge and skills.
- Open communication. Encourage open communication and feedback loops, creating a safe environment for employees to voice concerns and suggest improvements.
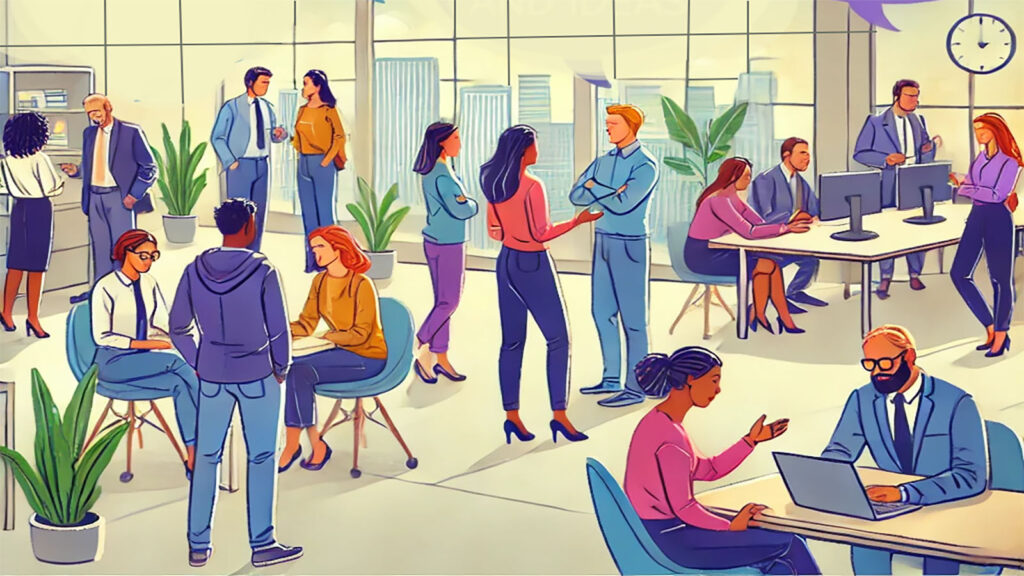
Continuous improvement and learning
- Quality management system (QMS). Implement a robust QMS that promotes continuous improvement through processes like root cause analysis and corrective actions.
- Ongoing training. Offer ongoing training, knowledge-sharing sessions, and opportunities for professional development related to quality.
- Celebrate successes. Recognize and celebrate quality successes, reinforcing positive behaviors and motivating others.
Quality-focused processes and systems
- Integrated quality checks. Integrate quality checks and controls into all processes, from design and development to delivery and customer service.
- Technology and automation. Leverage technology to streamline quality assurance activities and enable real-time monitoring.
- Supplier management. Establish robust supplier management processes to ensure quality standards are maintained throughout the supply chain.
Performance measurement and feedback
- Balanced scorecard. Implement a balanced scorecard to measure and track quality performance metrics at various levels.
- Data analysis. Regularly review and analyze quality data to identify trends and areas for improvement.
- Constructive feedback. Provide timely and constructive feedback to reinforce quality-focused behaviors and promptly address issues.
Conclusion
Scaling a workforce while maintaining quality demands a strategic focus on continuous training, quality control, technology integration, and a culture of excellence. Some key approaches include:
- Quality standards and benchmarks. You should establish clear metrics like defect rates, customer satisfaction, and regulatory compliance. Use these to consistently measure and track quality.
- Strategic staff augmentation. Pay attention to eliminating skill gaps by selecting top-tier talent through rigorous screening. Ensure effective integration with clear roles, expectations, and thorough onboarding.
- Leveraging technology. Implement digital quality management systems with features like centralized data repositories, automated workflows, real-time analytics, and compliance tracking. Utilize AI and data analytics for defect analysis, process optimization, and predictive maintenance.
- Continuous training programs. Conduct regular skills assessments, promote a culture of learning, leverage technology for flexible training delivery, and continuously improve training content based on feedback.
- Developing a culture of quality. Foster leadership commitment, engage and empower employees, implement a robust quality management system, integrate quality checks into all processes, and use performance measurement tools to monitor and improve quality.
Outsourcing companies, it’s time to embrace these strategies to scale your workforce effectively without compromising on quality. By adopting these best practices, you can ensure that your growth is sustainable, your teams remain skilled and motivated, and your projects consistently meet the highest quality standards.
Quality should be a core value embedded in every aspect of your operations, and with the right approach, you can expand your software development capabilities while maintaining the excellence that defines your success. Commit to these strategies, and watch your organization thrive in a competitive marketplace, delivering superior results that exceed client expectations.
Egor Kaleynik
IT-oriented marketer with B2B Content Marketing superpower. HackerNoon Contributor of the Year 2021 Winner – MARKETING. Generative AI enthusiast.
Featured in: Hackernoon.com, Customerthink.com, DZone.com, Medium.com/swlh
More info: https://muckrack.com/egor-kaleynik